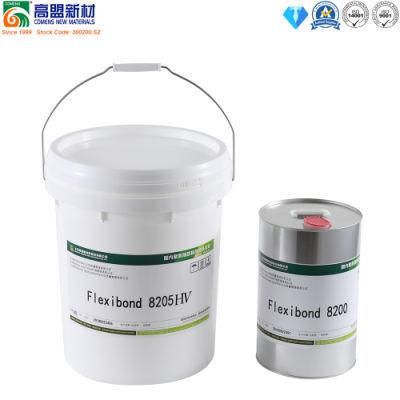
Two Component Polyurethane Adhesive for Van Truck and Refrigerated Box Sandwich Panel Bonding
Beijing Comens New Materials Co., Ltd.- Type:Polyurethane Adhesive for Sandwich Panels Bonding
- Material:Polyurethane Adhesive
- Bonding Faction:Structural Bonding Adhesive
- Application:Automobile
- The Color After Mixing:Light Yellow
- Mixing Ratio (by Weight):5:1
Base Info
- Model NO.:Flexibond 8205HV
- Shear Strength:≥ 10MPa (Aluminum Alloy)
- Shelf Life (Resin):12 Months
- Shelf Life (Hardener):6 Months
- Curing Mechanism:Poly Addition
- Transport Package:Pallets,Pails
- Specification:25kg+5kg Pail, 1250kg+250kg,Drum
- Trademark:Flexibond
- Origin:China
- HS Code:3506919090
- Production Capacity:30000tons,Year
Description
≥ 10Mpa (Aluminum alloy)Shelf life (unopened below 25) 12 months 6 months
Application:(1) Preparation:
Prepare an empty drum. Request: clean and dry. Mixing tool: Sticks for manual mixing or electric mixer. Electronic scale: It would be better if the electronic scale can accurately weighting to a decimal point.
(2) Surface Treatment of the Substrates: The substrates should be clean and dry and of no grease, dust, or other contaminations. The substrates can be cleaned by ethanol, acetone. If the metal surface is coated with primer, the discharged agent on the plastic surface is cleaned, or the surface is polished, the adhesion can be increased significantly.
(3) Flexibond 8205HV/Flexibond 8200=5:1 (by weight) Mix for 1-2 more minutes after the two component color is well mixed. Use up the mixer as soon as possible before its pot life, or less frequent principle can be taken.
(4) Adhesive Coating: The adhesive can be coated with serrated scrapers manually or rollers. The adhesive should be coated uniformly on the substrate surface. The recommended dosage is 300-600g/m2. The dosage varies with the roughness of the substrate surface. The adhesive should be coated within its pot life. The specifications can be referred to Figure 1.
(5) Pressing: Substrates have been coated with adhesive should be pressed within open time, or the adhesion strength will be affected. Raise the compounding pressure as high as possible without affecting the material forming. The specifications can be referred to Figure 1.
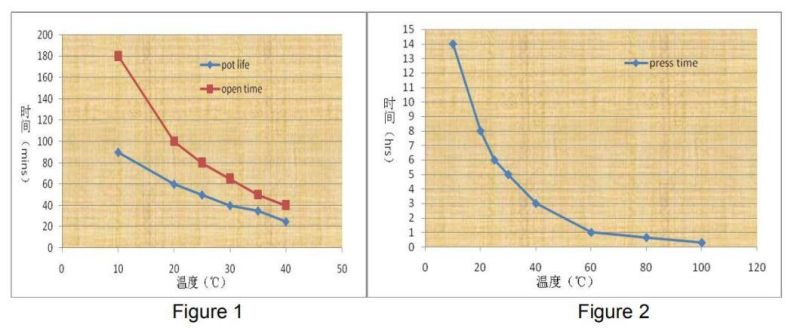
(6) Pressing time The curing speed and the time to form adhesion vary with the temperature. The curing speed is slower and it takes longer time for pressing as the temperature is lower; the curing speed is faster and it takes shorter time for pressing as the temperature is higher. The pressing time is 5-8 hours under 23ºC. The fully cured time is 7 days. The specifications can be referred to Figure 2.
(7) Working Condition Recommended working condition: temperature 5-30ºC, relative humidity <80ºC. The curing speed will be affected if the temperature is too low. And too much bubble will be formed if the humidity it too high.
(8) Clean Recommended Cleaner: acetone, butanone
Specification:
Resin(Flexibond 8205HV): 25.0kg/pail
Hardener(Flexibond 8200): 5.0kg/pail
The packaging can be adjusted according to customer's requirement.
Shear Strength Chart:
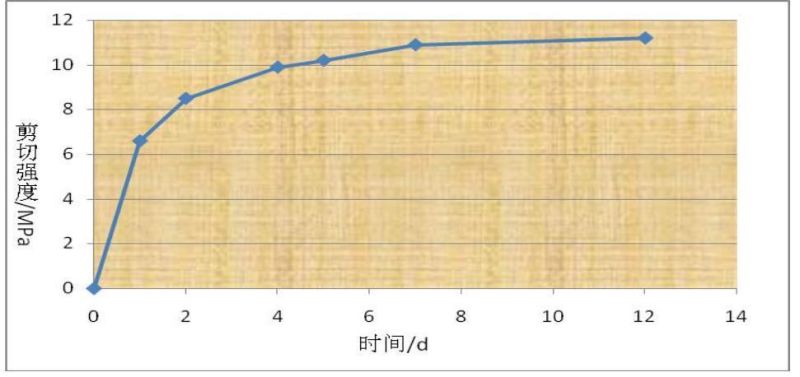
Partners:
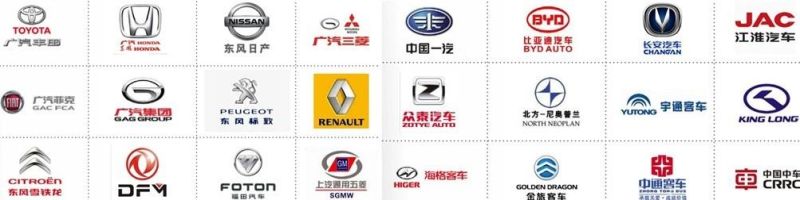

Company Profile:
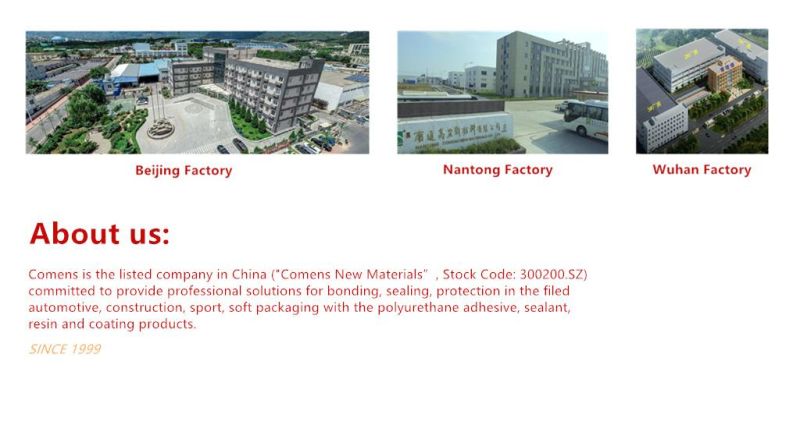
Production Base:
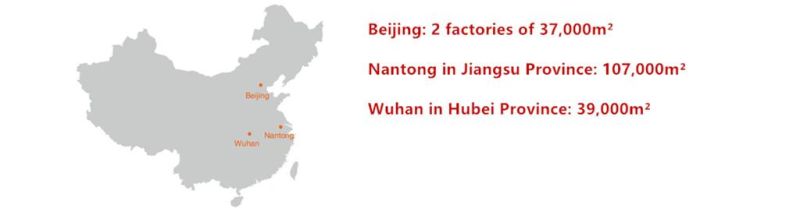
Automatic Production Lines and Quality Assurance:
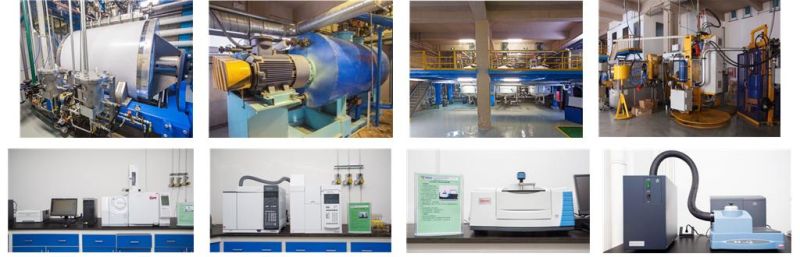
Global Sales Network:
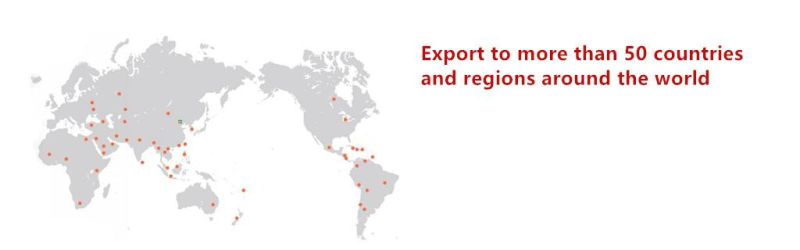
Certificates:
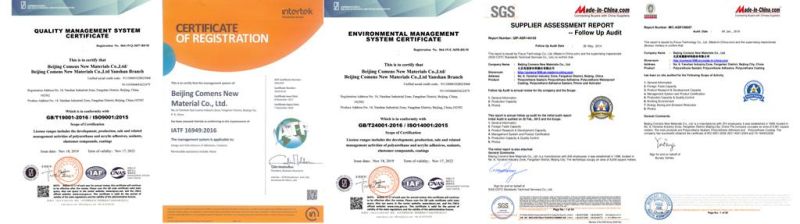
COMENS,A FULL RANGE OF SOLUTIONS
FOR MULTIPLE INDUSTRIES
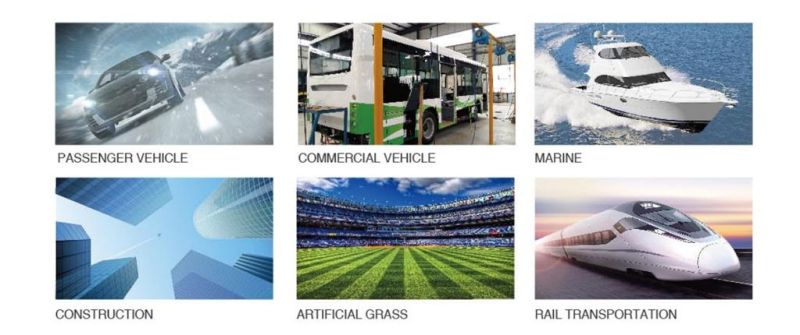
Application:(1) Preparation:
Prepare an empty drum. Request: clean and dry. Mixing tool: Sticks for manual mixing or electric mixer. Electronic scale: It would be better if the electronic scale can accurately weighting to a decimal point.
(2) Surface Treatment of the Substrates: The substrates should be clean and dry and of no grease, dust, or other contaminations. The substrates can be cleaned by ethanol, acetone. If the metal surface is coated with primer, the discharged agent on the plastic surface is cleaned, or the surface is polished, the adhesion can be increased significantly.
(3) Flexibond 8205HV/Flexibond 8200=5:1 (by weight) Mix for 1-2 more minutes after the two component color is well mixed. Use up the mixer as soon as possible before its pot life, or less frequent principle can be taken.
(4) Adhesive Coating: The adhesive can be coated with serrated scrapers manually or rollers. The adhesive should be coated uniformly on the substrate surface. The recommended dosage is 300-600g/m2. The dosage varies with the roughness of the substrate surface. The adhesive should be coated within its pot life. The specifications can be referred to Figure 1.
(5) Pressing: Substrates have been coated with adhesive should be pressed within open time, or the adhesion strength will be affected. Raise the compounding pressure as high as possible without affecting the material forming. The specifications can be referred to Figure 1.
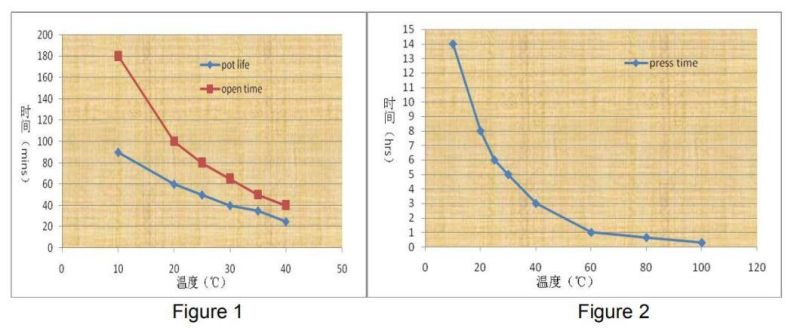
(6) Pressing time The curing speed and the time to form adhesion vary with the temperature. The curing speed is slower and it takes longer time for pressing as the temperature is lower; the curing speed is faster and it takes shorter time for pressing as the temperature is higher. The pressing time is 5-8 hours under 23ºC. The fully cured time is 7 days. The specifications can be referred to Figure 2.
(7) Working Condition Recommended working condition: temperature 5-30ºC, relative humidity <80ºC. The curing speed will be affected if the temperature is too low. And too much bubble will be formed if the humidity it too high.
(8) Clean Recommended Cleaner: acetone, butanone
Specification:
Resin(Flexibond 8205HV): 25.0kg/pail
Hardener(Flexibond 8200): 5.0kg/pail
The packaging can be adjusted according to customer's requirement.
Shear Strength Chart:
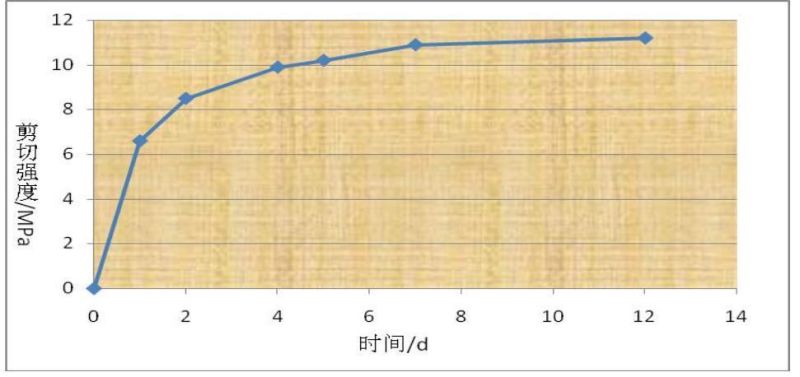
Partners:
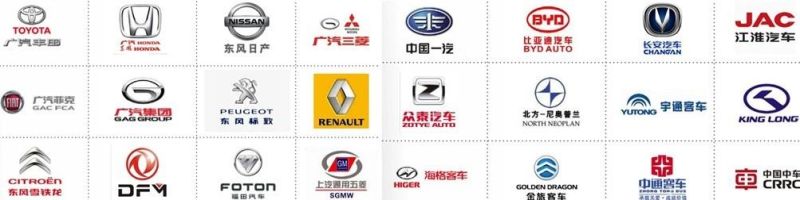

Company Profile:
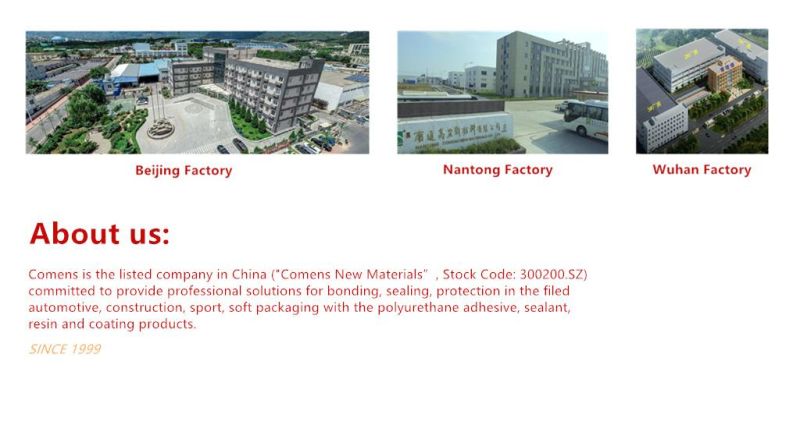
Production Base:
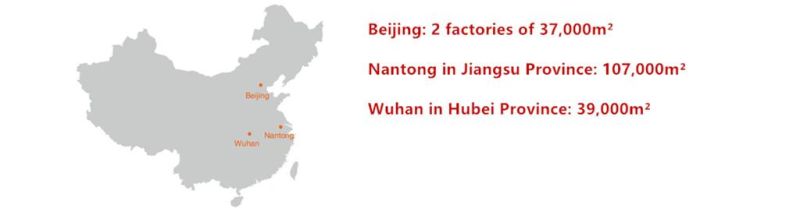
Automatic Production Lines and Quality Assurance:
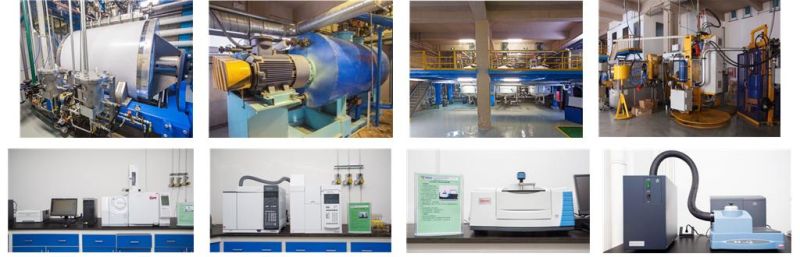
Global Sales Network:
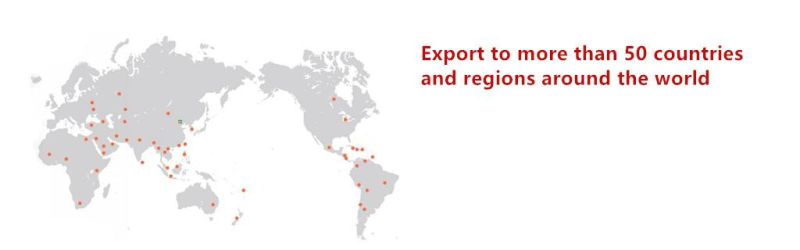
Certificates:
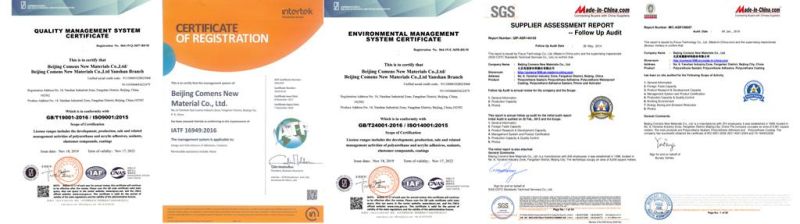
COMENS,A FULL RANGE OF SOLUTIONS
FOR MULTIPLE INDUSTRIES
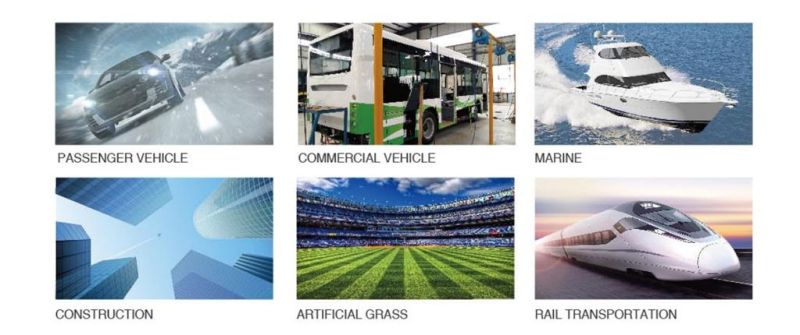